
Systems
2D Image Acquisition in Mono and Color
Goal of 2D image generation
2D mono cameras are a cost-effective and straightforward solution for a wide range of industrial applications. Their simple implementation and ability to generate a 2D image in a single shot eliminates the need for complex scans, encoders or drive systems.
These cameras are extremely compact and can be used as vision sensors or smart cameras, making them a versatile option for a wide range of applications.
The primary goal of 2D imaging is to clearly distinguish specific object features from their surroundings. A key aspect of this process is to generate the highest possible contrast. To achieve optimum results, the contrast must be significantly higher than the image noise. This ratio ensures that the smallest defects and features are recognised accurately.
With increasing contrast, the inspection not only becomes more reliable, but also more robust against changing environmental conditions and other interfering factors.
How 2D image generation works
We do not inspect the object, but in the vast majority of cases a digital 2D image of the object! Let´s have a look to this process.
1. Illumination of the object
The basis of every image acquisition is lighting. A light source emits light that falls on the object to be photographed. The quality and intensity of the light source influence the level of detail and clarity of the image.
2. Reflection of light
Part of the incident light is reflected by the object. This reflection is crucial as it contains information about the surface and structure of the object. Differences in the colour, texture and shape of the object influence how the light is reflected.
3. Optical depiction on sensor
The reflected light hits the lens, which images the object on the sensor. The lens focuses the light and thus determines the sharpness and detail of the image.
4. Detection of the photons
In the sensor, the incoming photons are registered by sensor pixels. Each pixel counts the number of incoming photons and generates electrical signals. The number of pixels and their arrangement affect the resolution of the image.
5. Digitisation of the information
The electrical signals from the sensor pixels are converted into digital information. This process involves quantising and processing the signals to produce a digital image. The quality and accuracy of the digitisation determines the level of detail and colour fidelity of the image.
Image acquisition

Generated mono8 image
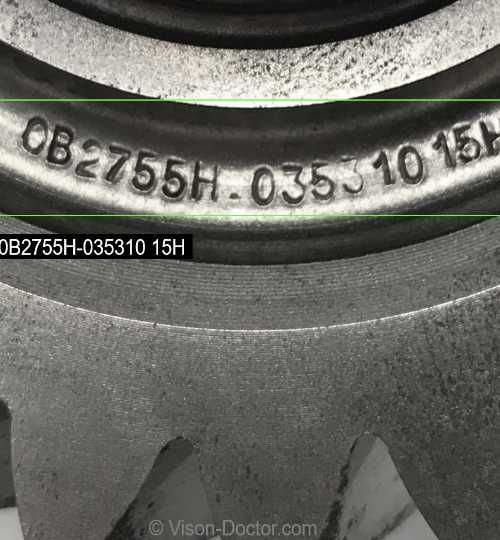
The digital greyscale image
Digitisation and visualisation
The electrical signals generated by the sensor are digitised and displayed as a 2D matrix. Each element of the matrix represents a pixel and stores the brightness information of the corresponding image area.
Processing the digital 2D image
The digital 2D image can now be analysed using image processing software algorithms. This software allows the brightness information to be analysed and processed to detect patterns, structures and other relevant features in the image.
Standard bit depth for image processing
In image processing, a standard bit depth of 8 bits is often used for monochrome images. This corresponds to 256 grey levels, where grey level 0: no photons, = black. Grey level 255 corresponds to fully saturated information = white.
Of course, there are plenty of applications where 10, 12 or 16 bits of greyscale information is used, but this is the exception rather than the rule, as uncooled standard 2D cameras rarely provide more than 8 bits of usable information. Finally, the additional information gain is often not really relevant for standard industrial inspections. Processing at 8 bits requires only two bytes per pixel, while 10 to 16 bits require two bytes. Memory consumption and processing times are always an issue in fast industrial processes...
Digital greyscale image
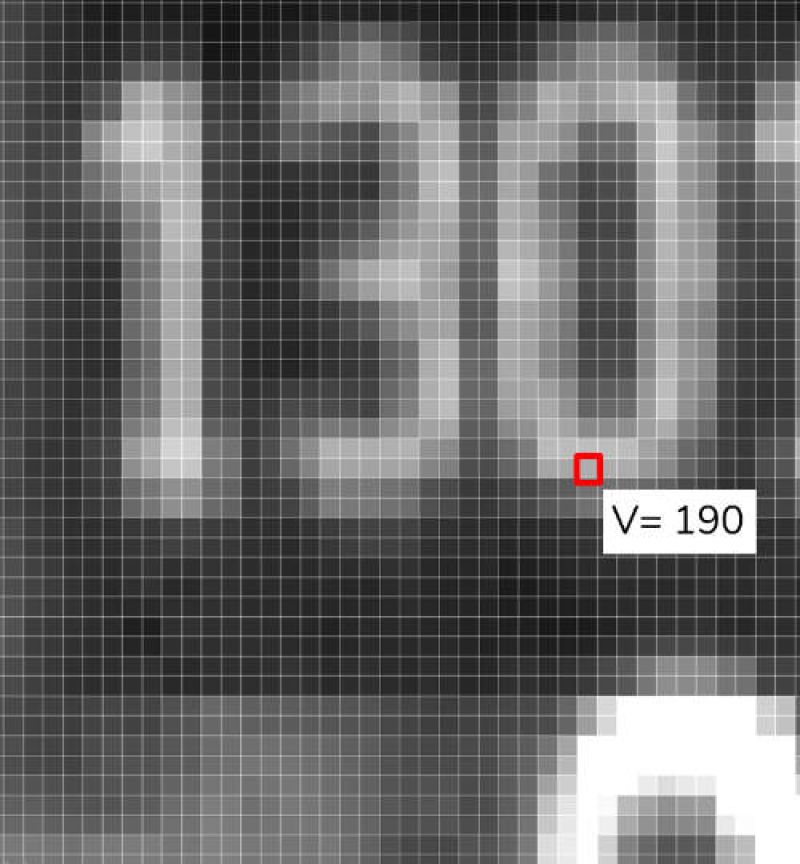
The digital colour image and colour channels
Colour channels in digital colour images
A typical digital colour image consists of three colour channels:
- Red (R)
- Green (G)
- Blue (B)
These three channels normally have a depth of 24 bits, with each channel using 8 bits. In special applications, 36- or 48-bit images can also be used to achieve a gretater colour depth and more accurate colour reproduction.
Alternative colour spaces
In addition to the RGB colour space, there are other colour spaces that are used depending on the application:
- HSV (Hue, Saturation, Value)
- Lab (L, a, b)*.
These colour spaces offer different advantages and are used to highlight or process certain aspects of the colour information.
Image processing algorithms and colour channels
Image processing algorithms can work with colour channels in different ways:
Full RGB colour information: uses all three colour channels to process detailed colour information.
Individual colour channels: Uses only one of the R, G or B channels for specific analyses.
8-bit monochrome: Reduces the image to a single channel with 256 grey levels to analyse brightness information.
Example:
The customer uses a colour camera to check the contents of a fuse box (see images). The colour inspection of the fuses is done with full colour depth (RGB, 24 bit), the object search for positioning and the reading of a barcode on a label is performed with only 8 bit data. This can be a mono8 image or a single colour channel.
Colourful object
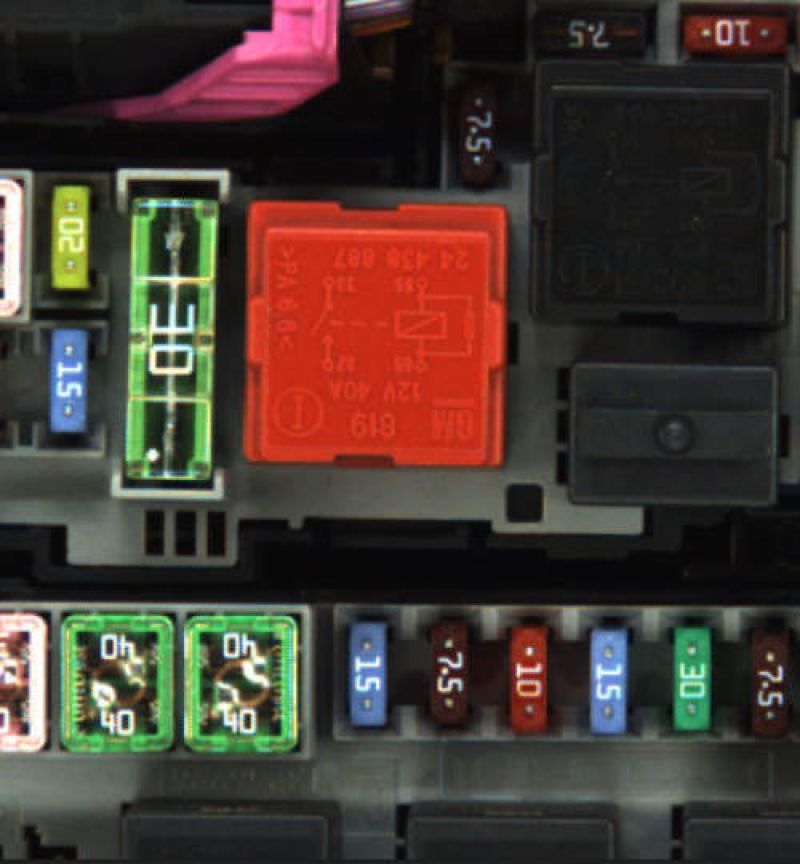
Mono8 & Color channels

Benefits of 2D Imaging (mono & color)
1. Cost-effective and simple
2D mono cameras are inexpensive to buy and operate. They are also easy to implement and do not require complex systems.
2. Simple image acquisition
A single shot is enough to create a 2D image.
No need for scanning, encoders or drive systems.
3. Compact design
2D mono and colour cameras can often be very compact (up to 24 megapixels).
They can be used as vision sensors or smart cameras.
4. Versatile resolutions
From VGA to 250 megapixels, 2D mono cameras offer a wide range of resolutions. This allows the camera to be optimally adapted to specific requirements.
5. Wide range of interfaces for industrial cameras
The cameras offer a wide range of interfaces including MIPI, USB3, GigE, CamLink and CoaxPress. This ensures easy and seamless integration into existing systems.
6: For colour cameras: additional object colour information
Monochrome and colour sensors are often available from the same manufacturer and usually cost the same as industrial cameras. Colour analysis is easy to implement.
Potential disadvantages (mono & color)
1. No height information (3D)
2D mono and colour cameras cannot capture 3D height information, which is a disadvantage for certain applications.
2. Non-ideal for long objects
The form factor of the sensor is often not ideal for capturing long objects, which can limit application possibilities.
3. Perspective distortion with cylindrical objects
Perspective distortion can occur when capturing cylindrical objects, making analysis significantly more difficult. Illumination is also difficult to achieve.
4. Unsuitable for web applications
2D mono cameras are often not the best choice for applications where continuous materials are processed.
5. Colour only: longer exposure times than mono cameras
Exposure times are typically three times longer than with monochrome cameras, which can result in slower processes.
6. Colour only: less image detail than monochrome cameras
Bayer colour reconstruction can result in a loss of image detail due to the need to interpolate colour information.
7. Colour only: More data
2D colour cameras generate three times more data than monochrome cameras, requiring more storage and computing resources.
Need help selecting a system?
Vision-Doctor.com is a private, independent, non-commercial homepage project and not a technology provider or system integrator. Suitable technologies and further professional support can be obtained from the companies & partners listed below.
If necessary, I will be happy to provide a quick recommendation, contacts and brief information.